DM Inspired
Daniel Murray's protfolio

SELECTIVE ELECTROPLATING
This project develops a process to produce circuitry inside a 3D printed part. By using dual material 3D printing with conductive and non-conductive filament, low current circuits can be produced. These circuits can be electroplated to produce electronic wiring suitable for robotics and high current applications.
INTRODUCTION
This project aims to further the advancement of 3D printing electronics and has the potential to advance industries such as wearable electronics, embedded electronics, 3D printed bioelectronics and space exploration. There are many methods to achieve 3D printed electronics including conductive filaments, pick and place of components during printing and conductive inks in material jetting printers. Each method has advantages and disadvantages, with the main problems being a reliable connection, software support and expense.
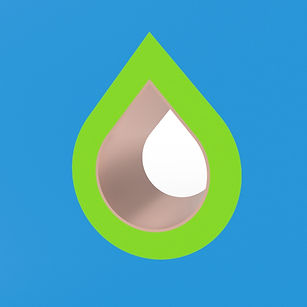
Using a FDM dual material printer to print conductive channels that are electroplated to produce minimal resistance connections. A potential design for conductive channels is shown in the left image, with the blue areas being non-conductive plastic and the green being conductive scaffolding for the electroplated connection. Electroplating could overcome the issue conductive filaments have with a potential break in the connection. Each layer of newly deposited metal, in time, could bridge the gap to regain connection, the right animation.
PROJECT AIMS
This project aims to produce minimal resistance connections inside of a fused deposition modelling (FDM) printed part. To achieve minimal resistance, the connections must have a resistance lower than 50Ω over a 100mm sample. The best performing samples will be repeated 5 times to check for reliable connections. The objective of this project is to produce parts with minimal resistance connections by changing the following variables:
-
Electroplating voltage (V)
-
Electroplating temperature (oC)
-
Electroplating tank agitation (rev/min)
-
Electroplating distance between the anode and cathode (mm)
-
Printer line width (mm) • Printer layer height (mm)
The measurables are rated out of 5:
-
The area covered by the plate
-
The strength of the chemical bond
-
The amount of electrically dead areas or connection breaks, shown in the below video.
For this project to be a success:
-
Resistance of a 50mm length must be lower than 50Ω
-
Coverage must have a 5 rating
RESEARCH
The full research relating to this project can be found inside the project paper. the following information is the necessary research that's needed to understand the results of this project.
Benefits to 3D printing electronics:
-
Simplified fabrication
-
Increased design freedom
-
Novel form factors
-
Reduced weight
-
Reduced wastage
-
Reduced production time bottlenecks
-
Lower prototyping and fabrication costs
ALREADY ESTABLISHED METHODS TO 3D PRINT ELECTRONICS
REASON MINAMAL RESISTANCE IS NEEDED FOR ROBOTICS
Typical values for current, length and radius of 1Amp, 50mm and 1.5mm

FOR COPPER

FOR CONDUCTIVE FILAMENT

EXPERIMENT SET-UP
Samples of 50mm in length were printed on a Ender 3 from conductive filament produced by MSNJ with a resistivity of 1.0x10-3 Ω⋅m when compared to copper of 1.7x10-8 Ω⋅m. Gloves were used when handling samples, this was to minimise adding oils to the plating surface. The test samples were then prepared to be plated this could involve being cleaned or sanded. The printed test samples were immediately added to a custom-built electroplating tank, this reduced human contact. The initial custom-built tank design had to be changed, so the variables could be controlled more reliably. The electroplating tanks were designed to accommodate variable ranges discovered in preliminary testing. Once the test samples had been plated, resistance, coverage, connection brecks and chemical bonds were recorded.
EXPERIMENTATION

T1 is based off metal plating and assuming the further the electrode distance the better the plate. T2 then tries to get more power to the cathode, T3 also tried to increase the power at the cathode. T3 was the first test sample to be rotated, and this was an improvement towards the goals of this project. T4 had handles so all metal was outside the electrolyte. T5 was placed closer to the surface. T6 put what had been learnt all together, closer to the anode, close to the surface and rotated around of the centre of the test sample. All the test samples so far struggle for coverage, T7 drops to volage to increase the time, in hopes to improve plating coverage. T8's setting go towards a smooth surface encase that was the reason for poor coverage. T9 increased the current above the range that was first thought, this was because it was noticed that coverage was improved when electrical arcing was happening at the cathode. T10 dropped the voltage to increase simpler to the theory behind T7.
To understand the full thought process behind each test sample, please read the experiment section (3.3) inside the project paper
RESULTS
Main points:
-
Apart from T2 all resistances decreased
-
T3, T6 and T9 were break throughs
-
T4 and T7 were a step backwards
-
T6 was the first breakthrough in coverage and therefore resistance
To validate the results a repeatability study was undertaken, by repeating the best preforming test sample 5 times. All 5 test samples had a final resistance less than or equal to 50Ω, as specified in the aims of this project. Out of these 5 repeated tests, T9.2 was the worst preforming test sample as it was only able to cover between 40-60% of the test sample. The drop in coverage is believed to be from a raise in environment temperature over 34 degree and therefore raising the temperature of the electrolyte, above the temperature set by the tank heater. T9.5 was the first test sample to achieve the top band rating in chemical bond, coverage and connection breaks, it was also the first test sample to have a resistance lower than 1Ω.
A CASE STUDY
A circuit was produced using the variables from the T9 test sample. A 12V power supply was connected by 2 70mm 3D printed tracks, with a cross section of 5mm by 5mm, to a 9V-12V strip light. When the strip lights were connected by only the conductive filament, the lights did not turn. Using a multimeter a voltage of 0.04V was measured across the strip lights, which is not inside its functional range (9V-12V). 11.96V were taken by the resistance of the 70mm connections. The 70mm tracks were then electroplated and connected to the 9V-12V strip lights. A multimeter measured 11.86V across the strip lights, which is inside their functional range of 9V-12V, hence the lights turned on. The plated copper allowed more voltage to reach the strip lights, compared to the 0.04V with just the conductive filament carrying the current.
DISCUSSION AND CONCLUSION
-
T6, T8, T9 and T10 had resistance less than 50Ω
-
T9 and T10 have a coverage higher than 80%
-
T9 reduced the resistance from 4400Ω to 2Ω
-
A completed 5-time reliability study with a standard deviation of 19Ω

The results of this project show that it is possible to use electroplating to convert 3D printed conductive filament to minimal resistance circuits. the above graph shows the correlation between coverage and connection breaks, proving that electroplating the conductive filament can overcome breaks in connection. Excluding T8 all printer setting were the same and therefore would have started with theoretically the same amount of electrically dead area. The results of this experiment show that as the plated area increased, the amount of electrically dead areas decreased. If electroplating was not bridging the gap across connection breaks, each test sample would have had the same amount of electrically dead area, the graph shows this is not the case.